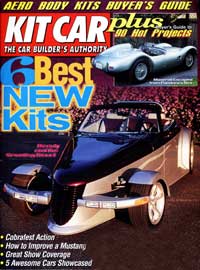
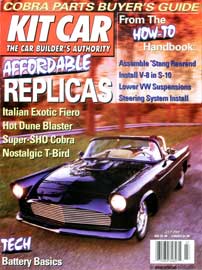
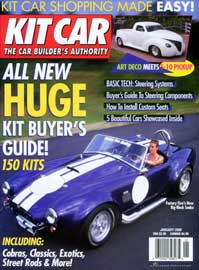
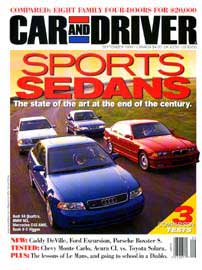
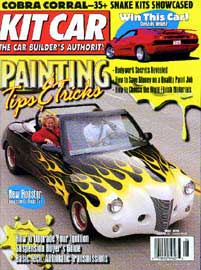
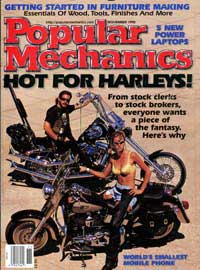
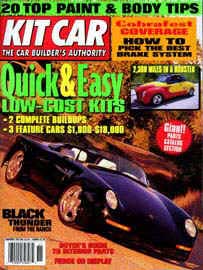
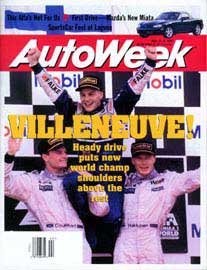
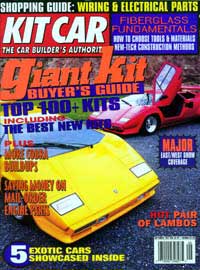
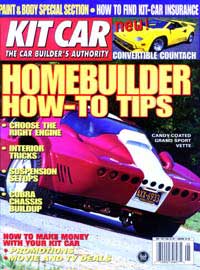
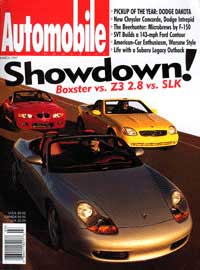
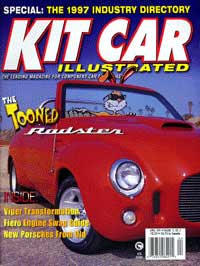

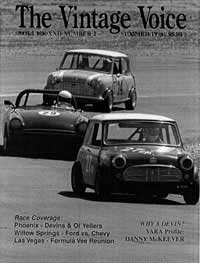
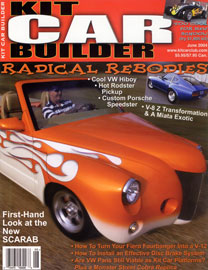
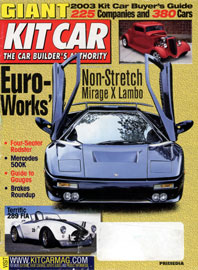
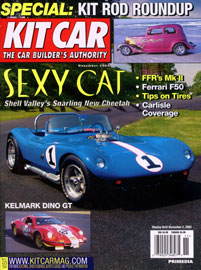
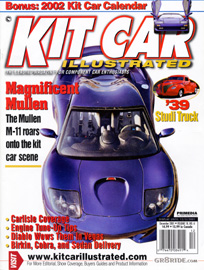
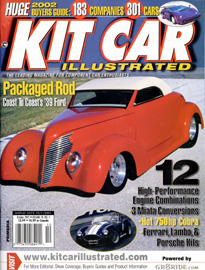
|
What
is Kit Car Magazine saying about the Rodster® Street
Rod?
Kit
Car Magazine
The Tri-Rodster Project
text by Jim Youngs
photos by Kaci Colton, Mark Wiley, Kerri Wiley, Carolyn Youngs, Jim Youngs
Alternately referred
to as the chop shop, the Rodster production line, or an Amish
car raising, it took a village to build three cars in one week.
It all began quite innocently
enough, as many car-project ideas germinate around here. Bench-racing
sessions typically generate lots of "why couldn't we" discussions,
and a few of them eventually lead to neat projects and great stories.
Few of these ideas in my experience, however, are as ambitious and span
as long a time period as the cool buildup project I'm about to outline
here.
Though
I've been involved with hotrods since high school, I credit my buddy
Mark Wiley with getting me really involved. About the time I
started freelance writing for Kit Car, Mark dragged me along
to the NSRA Rocky Mountain Nationals in Pueblo, Colorado, in the back
of his well-traveled '39 Dodge rod. Mark, like most rodders, is always
discussing future projects and is never at a loss for considering that
next cool car, much to the chagrin of his tolerant spouse.
Mark joined Henry Caroselli
(creator of the S-10 Blazer-based Rodster) and me for part of the Hot
Rod Power Tour in 1997. Of course, the topic of conversation invariably
got around to future projects. After a couple days hanging with Henry
and his long-haul Rodster, Mark was hooked, particularly when he learned
the Rodster kit would also easily fit a Typhoon donor. The wheels were
already in motion, and Mark quickly became a Rodster prophet, spreading
the word to all who would listen. He even bought a Typhoon ostensibly
on which to build a hot Rodster, but ultimately decided against cutting
it up. His desire to build a Rodster didn't wane, however. After more
than a year of thinking about it, he called me out of the blue one day
and asked what I thought about him and a bunch of his apostles building
several Rodsters all at the same time. I agreed it would make a good
story, and away Mark went with my encouragement.
Considerably
more time passed, and Mark continued to talk about the multi-Rodster
buildup, but time, family, and financial commitments kept the project
in the talking stage. Last summer, Mark called again and asked what
I thought about a two-car build. He had apparently convinced two of
his business associates to buy into the idea, one of whom dropped out
unexpectedly. I recall my comment to be, "Yeah, that would still
be a cool story, but three cars might just make it a cover story,"
or something like that. In the meantime, Mark and son Kent found an
S-10 donor in Kansas, towed it to Texas, and ordered their Rodster kit
from Henry. Likewise, Ray Yauk, an associate of Mark's, ordered his
Deluxe Rodster kit and found a nice GMC S-15 Jimmy in his hometown of
Buffalo, Oklahoma. They would still work toward finding someone to play
third string. Mark exhausted his contacts and approached me once again
with a new idea he had cooked up with the Rodsterfather: The three of
us would chip in parts and pieces of the third car, do the story, sell
that car at the end of the project, and recoup our individual investments.
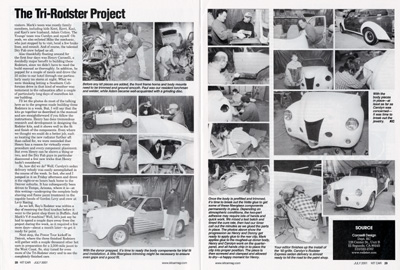
Having a considerable investment
in a bunch of my own project cars, I was pondering this latest idea
when my wife, Carolyn, asked at dinner one evening out, "How's
Mark's Rodster project coming along?" I explained where the project
stood and Mark's latest idea. She then began to ask some detailed questions
-- the answers to which would provide much more information about kit
cars than she usually cares to know. "How much would it cost to
build this third Rodster?" "How long would it take?"
"Would Henry be there to help?" "How hard is it to put
the kit together?" and on and on.
I only had one question of
her: "Why do you want to know all that?" Her short answer
centered on wanting to figure out what this attraction between men and
custom cars was all about. She also said she wanted to learn more about
my passion for cars, and then confessed that she had loved the Rodster
ever since I brought one of Henry's demonstrators home for a weekend
of cruising. She had several other compelling reasons as well, but I
must have missed some of them as I was drying my watery eyes (surely
caused by the smoky restaurant atmosphere).
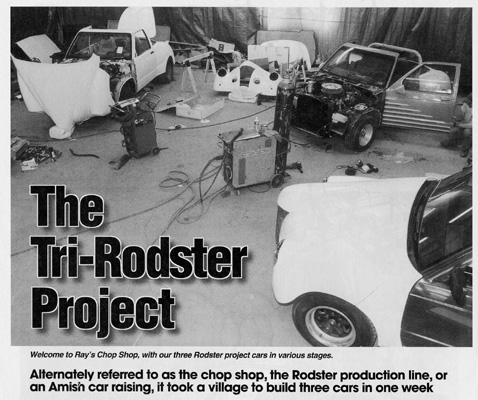
Now the story was taking
on an entirely new personality and much wider appeal. Carolyn committed
to building the third car, as well as volunteering it to be the official
Kit Car ride for the 2001 Power Tour, on which she would join
the Long Haul Gang from Detroit, Michigan, to San Bernardino, California.
We ordered the kit and began
Mountain states search for a two-wheel-drive S-10 donor on which to
build a Rodster Express sedan delivery model. Guess what -- there's
not much call for 2WD trucks on this side of the Rockies, so we made
a special trip to California -- donor-car mecca -- where we found a
one-owner beauty that had been well cared for.
The plan was for three build
teams to convene in Buffalo, Oklahoma, in late January 2001 and spend
a week transforming three donors into hot rods -- two roadster versions
and a sedan delivery -- minus paint, of course. Buffalo was chosen because
Ray's business, Dry Fab, is housed in an old Chevy dealership that just
happened to have plenty of empty, heated space in which we could all
work. All three kits were delivered there, and the Dry Fab crew collected
all the hardware, special tools, paint, and miscellaneous goods needed
to complete all three Rodsters.
Now,
Buffalo is not what you'd call a big town, especially considering the
Greyhoud bus doesn't even stop there anymore and the stoplight was turned
off some time ago. It's quite a friendly town up there in the panhandle,
however, and word of our project got around quickly. Ray's shop became
quite an attraction for local visitors. It was alternately described
as everything from a chop shop, to the Rodster production line, to an
Amish car raising. We even made the newspaper and were graciously welcomed
at restaurants in two towns and a motel in Woodward, Oklahoma, as we
contributed generously to the economy. We nearly cleaned out the True
Value Hardware store of rattle cans and drill bits.
Dry Fab is a metal fabrication
business specializing in oil and mining pipelines. As such, it's staffed
with talented metal fabricators, welders, and craftsmen and is loaded
with some of the coolest big tools you can imagine. It also houses a
well-stocked hardware section, all of which contributed greatly to our
project, particularly the skilled guys who went well beyond helping.
Henry designed the Rodster kit to be able to be assembled at home with
minimal tools, but items such as plasma cutters, MIG welders, hydraulic
shears, metal brakes, pneumatic nibblers, air riveters -- and the talented
guys who use them every day -- were most welcome.
We
roamed among the three donor cars to help as we could. After one team
completed a task, we went on to help the other two accomplish the same
procedure. In a kind of training exercise for Mark's Wiley Engineering
employees, the Tri-Rodster Project -- as he called it -- was set up
on a project management Gantt flowchart and each step on the three cars
was timed and logged. If you're interested in following along on the
whole project, log onto www.trirodster.com and enjoy.
Ray's Dry Fab team consisted
of son-in-law Paul, son Donny, and lots of frequent visitors. Mark's
team was mostly family members, including kids Kent, Kerri, Kaci, and
Kaci's new husband, Adam Cotton. The Youngs' team was Carolyn and myself.
Oh yeah, we also enlisted Mike the mechanic, who just stopped by to
visit, bend a few brake lines, and consult. And of course, the talented
Dry Fab crew helped us all.
Also thankfully floating
around for the first four days was Henry Caroselli, a decidedly major
benefit to building these Rodsters, since we didn't have to read the
build manual as thoroughly. In addition, he popped for a couple of meals
and drove the 35 miles to our hotel through one particularly nasty ice
storm at night. What we were thinking letting a Southern Californian
drive in that kind of weather was testament to the exhaustion after
a couple of particularly long days of marathon kit car building.
I'll
let the photos do most of the talking here as to the progress made building
three Rodsters in a week. But, I will say that the kits go together
as described in the manual and are straightforward if you follow the
instructions. Henry has done tremendous research and development in
designing the Rodster kits, and it shows well in the fit and finish
of the components. Even where we thought we could do a better job, such
as locating the new radiator further aft than called for, we were reminded
that Henry has a reason for virtually every procedure and every component
placement. But even Henry can be shown a thing or two, and the Dry Fab
guys in particular discovered a few new tricks that Henry hadn't considered.
So, how did we do? Well,
Carolyn's sedan delivery rebody was easily accomplished in the course
of the week. In fact, she and I jumped in it on Friday afternoon and
drove it the eight-or-so hours back home to the Denver suburbs. It has
subsequently been driven to Tempe, Arizona, where it is -- at this writing
-- undergoing the complete body shaving and flame paint treatment in
the capable hands of Gordon Levy and crew at Levy Racing.
As we left, Ray's Rodster
was within a day of receiving the final touches before it went to the
paint shop there in Buffalo. And Mark's V-8 machine? Well, let's just
say he had to spend a couple days away from the project during the week,
so it required a few more days -- about a month later -- to get it ready
for paint.
Next stop, the Power Tour
kickoff in Detroit, where the three finished Rodsters will gather with
a couple thousand other hot cars in preparation for a 2,500-mile jaunt
to the West Coast. So, stay tuned for even more of the Tri-Rodster story
and to see the completely finished cars.
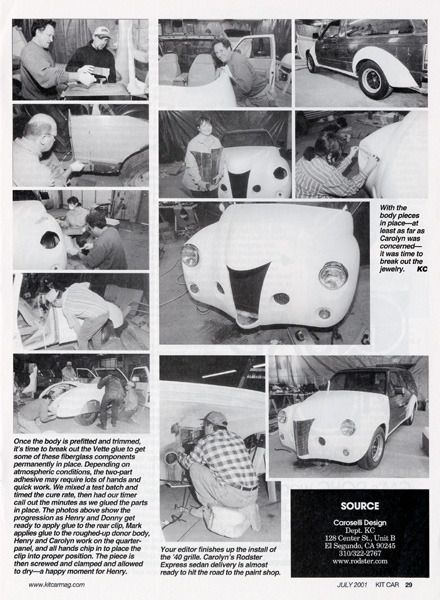
|